In the construction industry, builders, engineers, or contractors often prioritize cost-cutting when selecting sand for construction, opting for cheaper alternatives. However, they may need to pay more attention to the fact that using low-quality, inexpensive sand could lead to higher expenses in the future due to potential issues and complications caused by its subpar performance.
This article explores the critical issues and aspects of choosing quality sand and other raw materials in construction. We aim to explore the common misconception that using cheap sand can lead to significant financial savings without compromising on the quality of essential materials and can lead to a domino effect of hidden costs and delays.
The Significance of Quality Sand in Construction
A. Role of Sand in Concrete and Mortar Mixes:
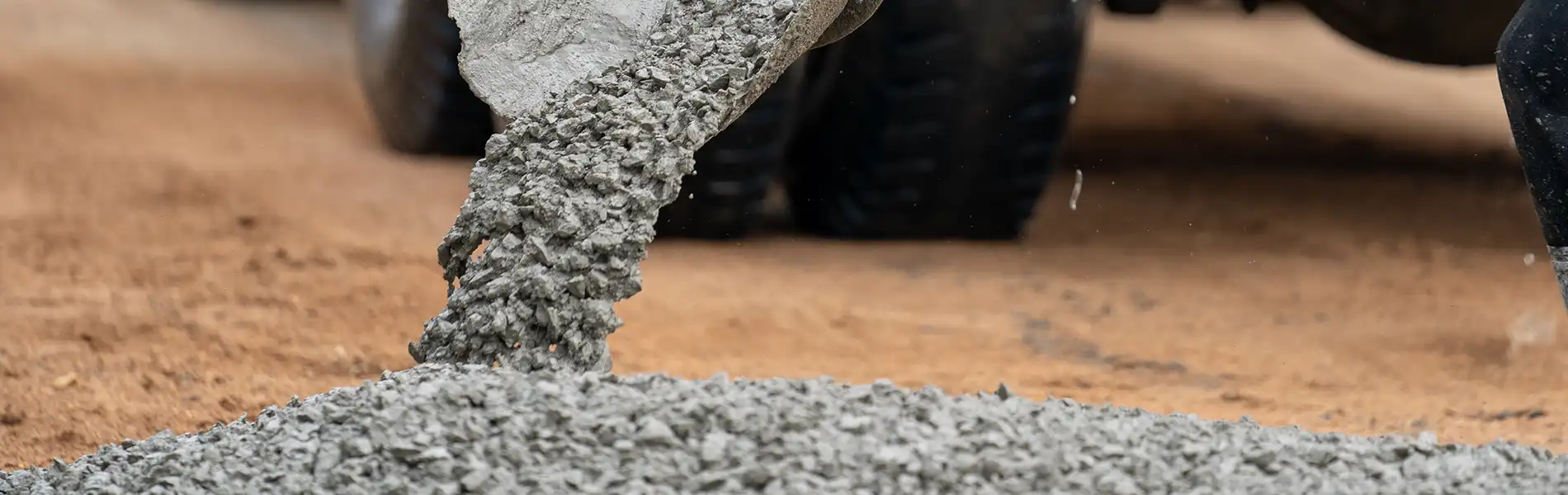
Sand is an indispensable ingredient in both concrete and mortar mixes. The sand acts as a filler in concrete, binding cement, and coarse aggregates together to create a solid and stable composite material. It contributes to compressive strength, dimensional stability, and resistance to weathering. Sand provides the necessary workability for skilled masonry work in mortar, ensuring a solid bond between bricks or blocks. With quality sand, the structural performance of concrete and mortar would be maintained, affecting the overall integrity of the construction.
B. Impact of Sand Quality on Structural Integrity:
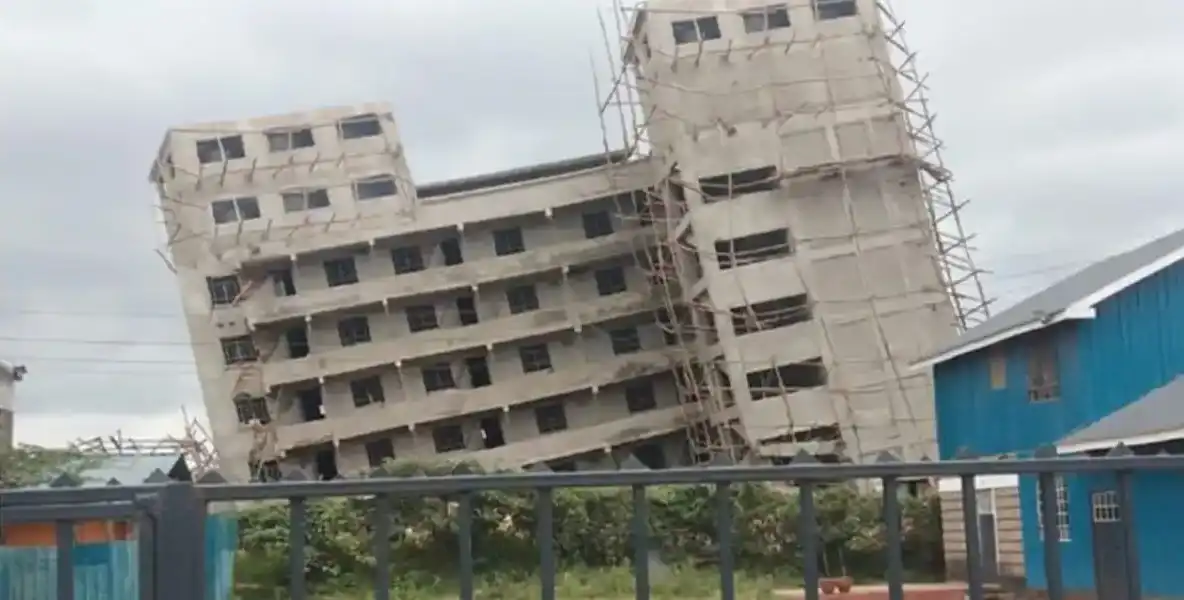
The quality of the sand directly influences the strength and durability of a construction project. Poor-quality sand often contains impurities like silt, clay, and organic matter, negatively impacting the bond between cement and aggregates. This, in turn, weakens the concrete or mortar, making the structure vulnerable to cracks, erosion, and structural failures over time. Choosing sand with the right particle size distribution and the absence of harmful contaminants is crucial to ensuring the longevity and stability of the building.
C. Importance of Workability in Construction:
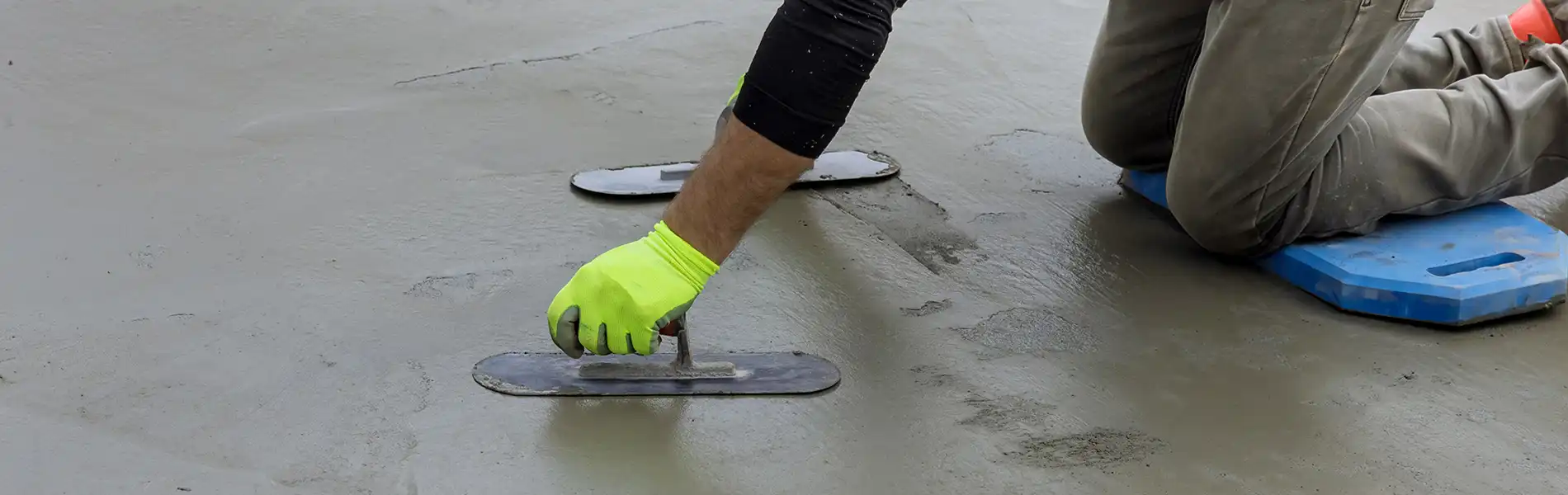
Workability is vital in construction materials, especially in mortar and concrete mixes. High-quality sand with well-graded particles enhances workability, making it easier for construction professionals to place, compact, and shape the material effectively. Adequate workability ensures that concrete can be poured and leveled easily, while mortar can be spread smoothly between bricks or blocks. Poor-quality sand with irregular particles can lead to difficulties in handling and finishing, resulting in subpar construction quality.
D. Avoiding Failures and Safety Hazards:
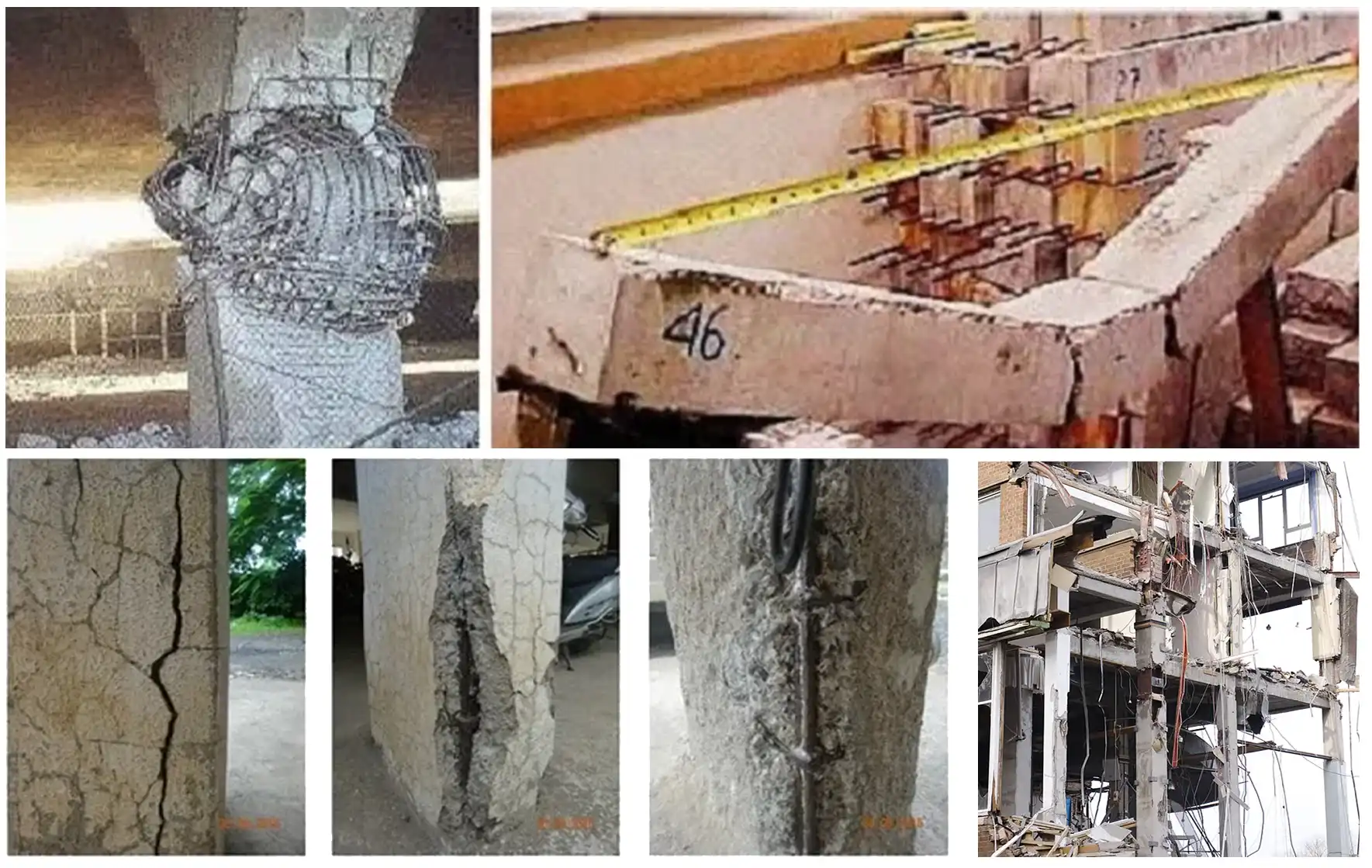
Using low-quality sand can lead to construction failures and safety hazards. As substandard sand lacks the necessary strength and bonding properties, it can lead to cracks, settling, and structural instability. Over time, these issues may escalate, jeopardizing the safety of occupants and causing costly repairs or reconstruction. Additionally, inadequate sand quality can compromise the structural resistance to seismic forces and other external stresses, posing further safety risks to the building and its occupants.
Understanding the True Cost of Low-quality Sand
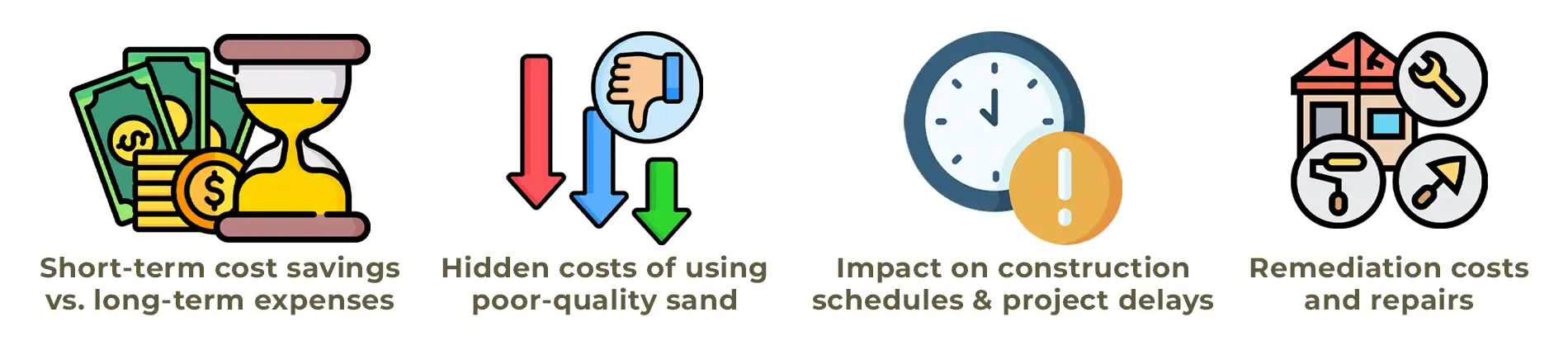
A. Short-Term Cost Savings vs. Long-Term Expenses:
Opting for cheap sand is a cost-effective decision in the short term, as it reduces the upfront expenses of a construction project. However, this apparent cost-saving measure often leads to higher long-term expenses. Poor-quality sand can compromise the structural integrity of the building, necessitating costly repairs, maintenance, or even premature replacements. The initial savings are outweighed by the extensive expenditures required to rectify the damage caused by substandard sand.
B. Hidden Costs of Using Poor-Quality Sand:
Using low-quality sand comes with hidden costs that are often overlooked during the decision-making process. Subpar sand may lead to decreased productivity on the construction site, as workers need help in handling and placing the material. This can result in increased labor costs and extended project timelines. Furthermore, the lower quality of the sand may require additional cement or other additives to compensate for its shortcomings, adding to the overall expenses.
C. Impact on Construction Schedules and Project Delays:
The use of poor-quality sand can lead to construction delays, directly impacting project schedules. As construction professionals grapple with the challenges of inadequate sand, delays may occur during concrete pouring, masonry work, and finishing stages. These delays add to the project's duration and incur extra costs associated with prolonging labor, equipment rentals, and site management.
D. Remediation Costs and Repairs Due to Substandard Materials:
One of the most significant costs associated with cheap sand is the need for remediation and repairs. Structures constructed with low-quality sand are prone to cracking, settling, and other structural issues. Addressing these problems requires extensive remedial work, which can be time-consuming and expensive. Additionally, the need for repairs may disrupt business operations or inconvenience occupants, leading to potential financial losses or legal claims.
Effects of low-quality Sand on Construction Performance
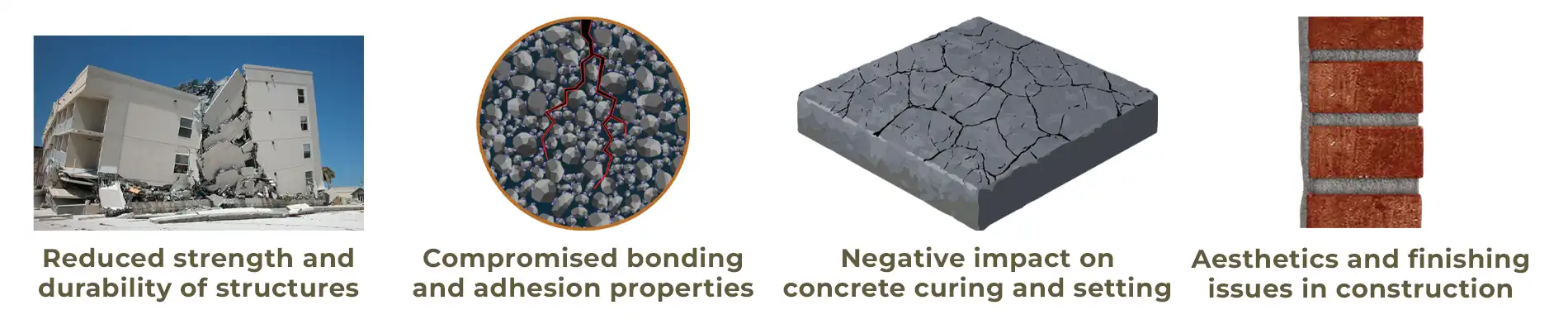
A. Reduced Strength and Durability of Structures:
Using cheap sand with inadequate particle size distribution and impurities can significantly reduce the strength and durability of construction materials. The weak bonding between cement and aggregates results in a less robust concrete or mortar mix, making the structure vulnerable to structural failures, cracking, and deterioration over time. This compromised strength can jeopardize the safety of the building and its occupants.
B. Compromised Bonding and Adhesion Properties:
High-quality sand with well-graded particles provides excellent bonding and adhesion properties, ensuring a strong and durable bond between construction materials. In contrast, cheap sand with irregular or poor-quality particles may fail to create a robust bond, leading to weak connections between bricks, blocks, or reinforcement. This lack of bonding can cause delamination and reduce the structural stability of the construction.
C. Negative Impact on Concrete Curing and Setting:
Proper curing and setting are critical stages in concrete construction to ensure optimal strength development and long-term durability. Cheap sand with a high silt or clay content can hinder water drainage and air circulation within the concrete mix, leading to improper curing and setting. This may result in a weaker concrete matrix with reduced compressive strength and increased vulnerability to environmental factors.
D. Aesthetics and Finishing Issues in Construction:
The quality of the sand also affects the aesthetics and finishing of the construction. Poor-quality sand may contain impurities that create surface discoloration, staining, or unevenness. This affects the overall appearance and can compromise the project's visual appeal. Also, rough surfaces caused by cheap sand can make finishing work challenging, leading to additional time and costs to achieve desired aesthetics.
Educating Clients and Stakeholders
A. Communicating the Importance of Quality Raw Materials:
Effective communication with clients and stakeholders is essential in educating them about the significance of using quality raw materials in construction. Construction professionals should explain how high-quality sand and other materials contribute to the building's strength, durability, and safety. Demonstrating the long-term benefits of investing in quality materials can help clients understand the value of making informed decisions for their construction projects.
B. Providing Transparency in Material Sourcing:
Transparency in material sourcing is crucial for building trust with clients and stakeholders. Construction professionals should be open about the origin and quality of the sand used in the project. Sharing information about suppliers, certifications, and testing procedures can instill confidence in the selection of reliable and reputable sources for raw materials.
C. Addressing Client Concerns About Costs:
Clients often have budget constraints and may be inclined to consider cheaper options, such as cheap sand, to save costs. Construction professionals should engage in open and honest discussions with clients about the potential risks and consequences of using substandard materials. Presenting a comprehensive cost-benefit analysis that includes long-term savings through enhanced durability and reduced maintenance expenses can help alleviate client concerns about costs.