Cinder blocks are hollow, rectangular building blocks made from cement and coal cinders / Fly Ash. They are mainly used in construction for various purposes, like constructing walls and foundations. Cinder blocks are lighter in weight, but they are not as strong and durable as solid concrete blocks. Cinder blocks are more prone to bowing, buckling, and damage, which will eventually lower strength and durability.
Note: In India, most people are not aware of the Cinder blocks; instead, they call them hallow blocks.
Materials Used in Cinder Block Production
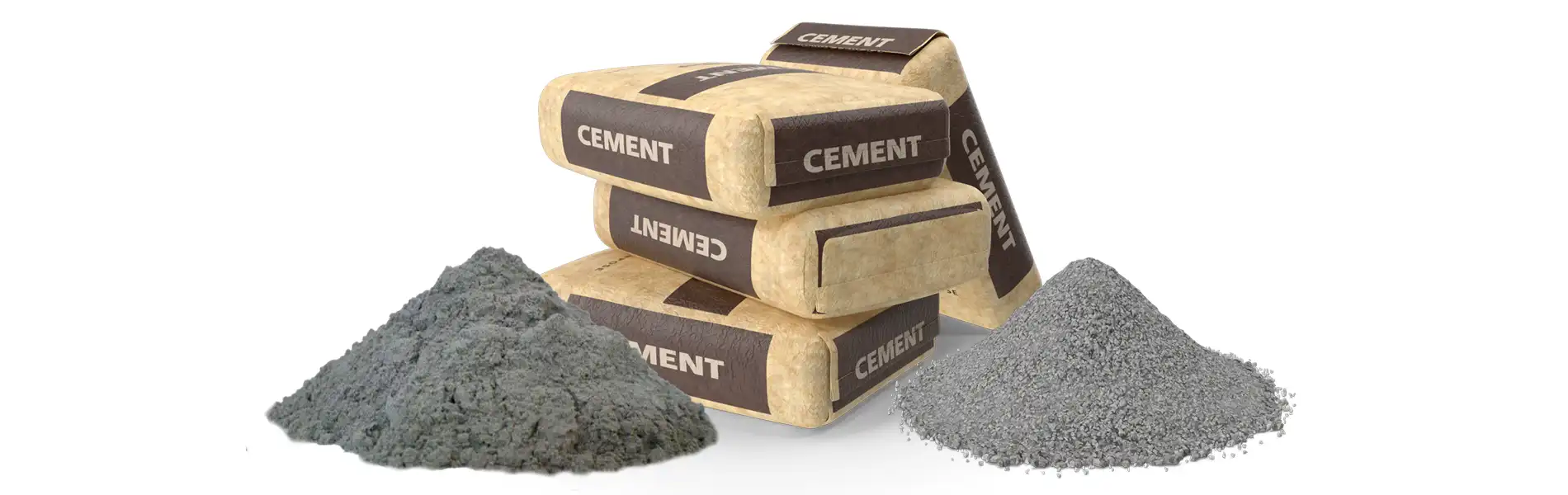
In the manufacturing of cinder blocks, several key materials are utilised:
-
Cement: It provides strength to the block.
-
Fly Ash / Coal Cinders: They are used as a substitute for sand and gravel, enhancing thermal insulation and sound-deadening properties and contributing to the block's structure and texture.
Manufacturing Process of Cinder Blocks:
The production of concrete blocks involves four main processes:
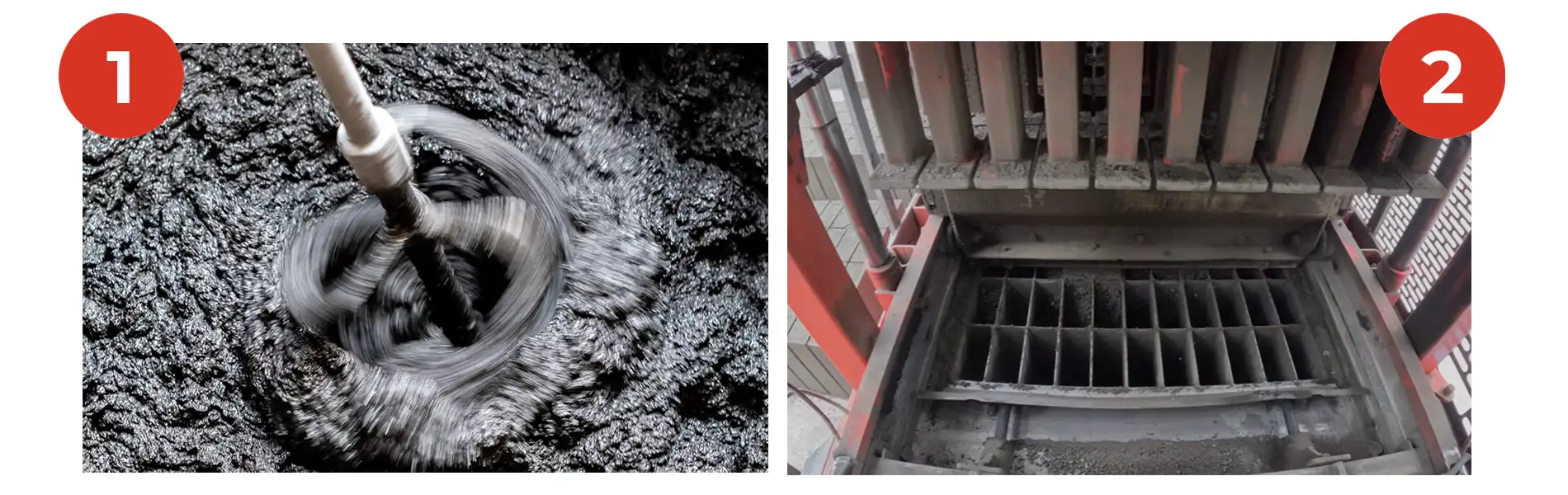
Mixing:
-
Raw materials are weighed and mixed in specific proportions using mechanical means.
-
Water is added to create a proper mixture, with colour pigments sometimes included.
-
The mixture is then poured into moulds for shaping.
Moulding:
-
The concrete block mixture is poured into moulds and compacted, often with the assistance of hydraulic pressure cylinders.
-
After compaction, excess material is removed, and the blocks are extracted from the moulds.

Curing:
-
The moulded blocks are sent to curing section for solidification, typically taking about 7 to 14 days.
-
Curing involves using steam at a specific temperature to harden the blocks.
Quality Control Measures:
-
A quality control team inspects samples from each batch to ensure consistency and adherence to standards.
-
Various types of concrete blocks are produced, each with unique compositions and characteristics, like lightweight blocks made from expanded clay, shale, or slate.
Structural Properties and Applications of Cinder Blocks
Structural Integrity and Load-Bearing Capacity:
-
The load-bearing capacity of cinder blocks varies based on their density, with denser blocks capable of withstanding around 2600 PSI of force. Higher-density materials contribute to increased load-bearing capacity, while ultra-cinder blocks can averagely withstand 500 to 1000 PSI.
-
Factors affecting load-bearing capabilities include the quality of materials, the presence of voids, installation techniques, engineering specifications, and structural design.
Note: Proper installation methods and adherence to safety standards are vital for optimising load-bearing performance.
Applications in Construction:
-
Walls: Cinder blocks are commonly used in constructing walls due to their durability and ease of assembly.
-
Retaining Walls: Cinder blocks are suitable for retaining walls, offering stability and strength in a few places based on the requirement.
-
Other Structural Elements: They are utilised in various residential, commercial, and industrial projects for columns, partitions, fences, and more.
Differences Between Cinder Blocks and Concrete Blocks:
-
The primary distinction lies in their composition. Cinder blocks use fly ash as a key component, while concrete blocks use it as a masonry unit.
-
Cinder blocks often have hollow areas to reduce weight, while concrete blocks can be solid or hollow, depending on the construction needs.
-
Concrete blocks are heavier but more durable and have higher compressive strength than cinder blocks.
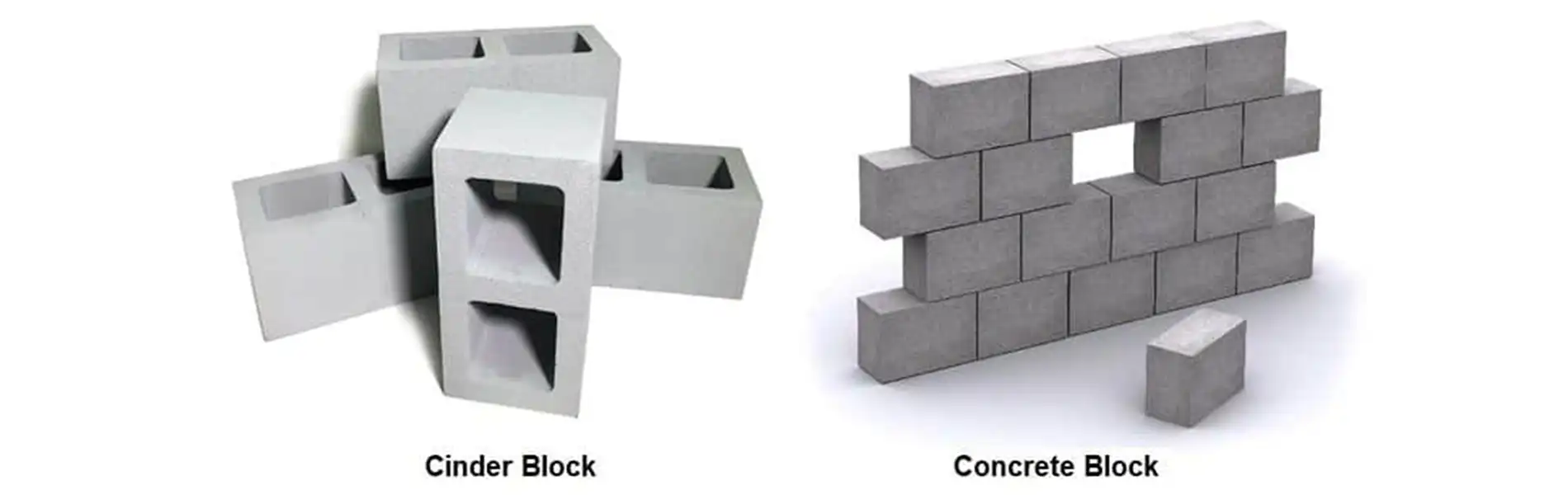
Difference Between Solid Blocks and Cinder Blocks
|
Cinder Blocks
|
Solid Blocks (Concrete Blocks)
|
Composition
|
Cinder blocks are made from concrete, sand, gypsum, and coal fly ash, or cinders.
|
Concrete blocks are made from Portland cement, water, sand, gravel, and sometimes crushed stone.
|
Appearance
|
They have a rough texture due to the cinder material from burnt coal or other combustible sources.
|
Have a smoother, more uniform surface compared to cinder blocks.
|
Weight
|
Generally lighter than concrete blocks due to their composition.
|
Heavier than cinder blocks due to the use of stone or sand in their composition.
|
Strength
|
They have lower strength compared to concrete blocks, making them more prone to cracking.
|
Superior strength and durability compared to cinder blocks, suitable for load-bearing functions.
|
Applications
|
They are commonly used in walls, foundations, and outdoor patios due to their affordability and ease of use.
|
Ideal for load-bearing applications like foundations, retaining walls, and other structural elements in construction projects. Also used in interior walls and floors due to their versatility and fire resistance.
|
Key Differences:
-
Aggregates: Cinder blocks use cinders from burned coal or volcanic pumice, while concrete blocks use sand or gravel as aggregates.
-
Weight and Density: Cinder blocks are lighter and less dense than concrete blocks.
-
Strength: Concrete blocks are stronger and more durable than cinder blocks, which are suitable for load-bearing functions.
-
Thermal Insulation: Cinder blocks have better thermal insulation due to their low density.
-
Aesthetics: Concrete blocks offer more options for colour, finish, and surface patterns compared to cinder blocks.
Cinder Blocks Vs Solid Concrete Blocks
When comparing cinder blocks and solid blocks (concrete blocks), both materials have distinct advantages and disadvantages:
Cinder Blocks:
Solid Blocks (Concrete Blocks):
Key Points:
-
Strength: Concrete blocks are generally stronger and more durable than cinder blocks, making them suitable for heavy construction purposes.
-
Cost: Cinder blocks are more affordable but offer lower strength compared to concrete blocks.
-
Applications: Concrete blocks are ideal for load-bearing functions like foundations and retaining walls, while cinder blocks are commonly used in non-load-bearing applications such as garden walls and landscaping projects.
Now that we have understood that Cinder blocks are not as strong and durable as solid blocks, we would recommend that you read this article to learn about solid blocks and check the below section to know where you can buy the best solid concrete blocks in Karnataka.
Solid Concrete Blocks in Karnataka
Alpha Concrete Blocks supplies high-quality blocks all over Karnataka. At Alpha Concrete Blocks, we never compromise on quality. Our plant is India’s largest fully computerised High-precision world-class block manufacturing plant. Alpha concrete blocks ensure that your building is protected from reduced strength, cracking and spalling, molding, and mildew growth. You are just a click away from protecting your house!! Click here to know more about Alpha Sand and order your concrete blocks right away.
Conclusion:
The selection of blocks depends on the type of construction project; however, solid concrete is ideally recommended. Happy construction.